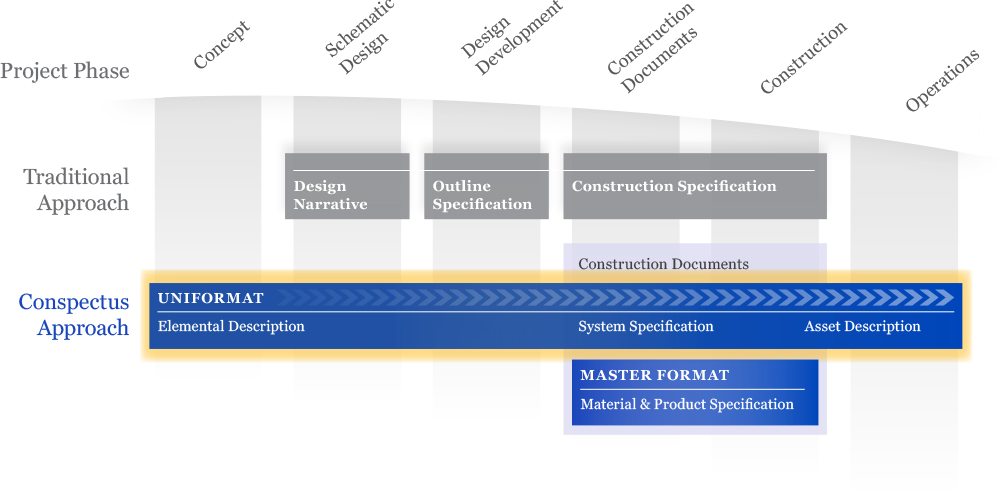
First published at Young Architects Forum Connection 16.01.
Construction contract documents consist of four items: the agreement, the conditions of contract, the drawings, the specifications, addenda, and modifications[i]. Each of the first four serves a distinct purpose. The agreement identifies the parties (owner and contractor), the scope, the time, and the cost. The conditions of contract set out the broad rights and responsibilities of the owner, architect, and contractor. The drawings identify the relationships and quantitative aspects of the project - everything that can be counted and measured. The specifications include administrative procedures and the qualitative aspects of the project - what products are required, how the products are installed, generally where the products are installed, and what performance must result. The last two simply modify the others, addenda before the contract is signed and modifications after the contract is signed.
Today's CSI 3‑Part Format[ii] construction specifications are organized with 6‑digit section numbers and titles in 50 divisions according to MasterFormat[iii]. The specifications describe work results - what the contractor must build to satisfy the contract. MasterFormat was originally introduced in the 1960s as a 5‑digit, 16‑division organization as a radical new idea. Then about 40 years later, in 2004, morphed to the current document. The change moved the content in the division order and expanded the available section numbers and titles for site work and mechanical, electrical, plumbing and fire protection engineering subjects. Plus the format added numbers and titles for process engineering subjects.
Industry acceptance took about ten years until commercial master specification systems stopped offering specifications in both numbering schemes. Change happens quickly - new formats, new standards, and new codes drive change. New ideas must evolve. Adoption of any change can lag until the incentive is obvious, especially if adoption is voluntary.
What comprises specifications today evolved from prior thinking about specifications and attempts to effectively organize data for construction contracts. And so too, today's specifications will evolve to better suit the industry needs. This paper will explore the idea of applying existing concepts and documents in a new way to produce a better result for the owners - those that bear all the risk of design and construction.
ASTM E1557 UNIFORMAT II[iv], an organizational structure for building elements, was created by economists and estimators to describe buildings by systems and assemblies. This organization allowed estimators to prepare costs of complete elements for analysis and comparisons of alternative elements early during the design process. The advantage was to enable informed decisions about building elements to remain within the owner's budget. Shortly afterward, CSI introduced the concept of Preliminary Project Description (PPD)[v], relying on UNFORMAT II organization, to describe a project during concept and schematic design phases, as the design was developed. CSI introduced its own version of UniFormat[vi] that included an introduction to collect information that applies to a project as whole such as program data, code requirements, and design criteria. For the remainder of this paper, the term Uniformat will be used to represent both the ASTM and CSI documents, collectively.
The notion of preliminary project description persisted and was formalized in PPDFormat[vii] that showed how to organize project data in a consistently structured way to describe elements by performance, design criteria, and individual components. The ASTM E06.81 Building Economics subcommittee[viii] responsible for ASTM E1557 praised the PPD concept from the beginning and continuously recommended its use in conjunction with preliminary cost estimates. Today estimators use Uniformat organization for early project estimates[ix]. Design teams rarely use a PPD, favoring design narratives without any industry recognized data structure, instead.
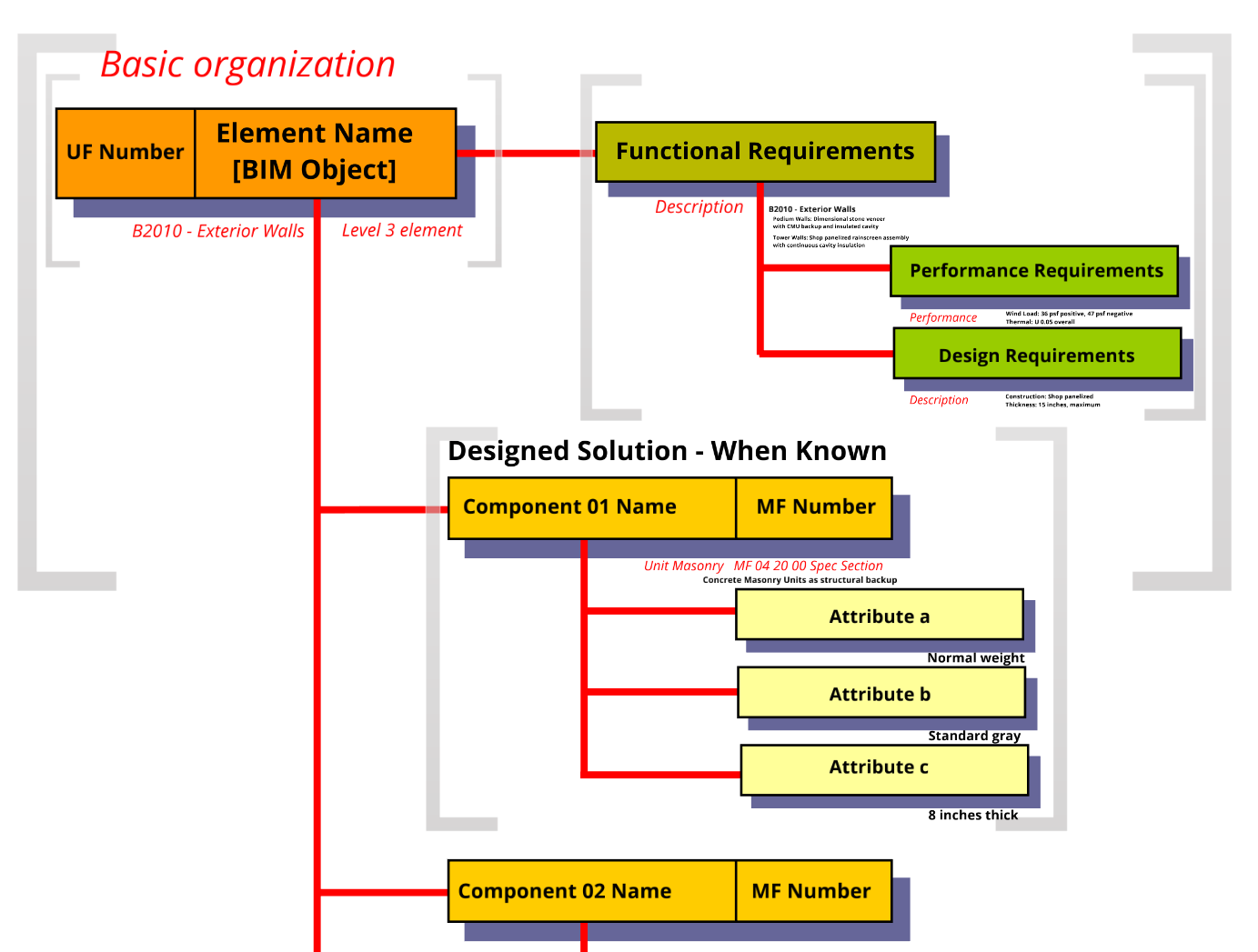
Meanwhile, at the turn of this century, USGBC introduced LEED and building commissioning[x]. Commissioning necessitated developing Owner Project Requirements (OPR) as the basis for performing building commissioning. OPR is a formalization of a project program to document design criteria and building performance.
The next evolution in specifications leverages all the existing organizational formats and resulting documents including OPR, PPD, Uniformat, and MasterFormat, but uses them in a new way. Let's begin with Uniformat specifications to describe the building elements, overlay MasterFormat construction specifications to buy and install the components comprising the elements, and name both sets of specifications as contract documents to incorporate the complete project qualitative requirements.
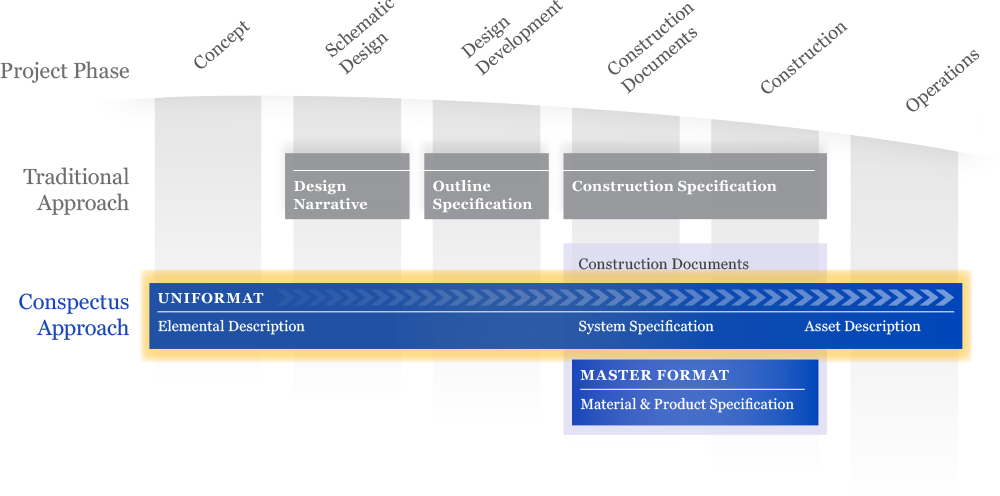
Estimators recognized Uniformat's usefulness during the early design phases[xi]. CSI recognized its usefulness as the structure for PPDs to collect and document design criteria and OPR before the design is actually started. Day one, when the owner decides a building is needed, start the data collection. What is the program - what spaces are required, what occupants and processes must be accommodated? There is a place for all of this in Uniformat. Say what you know, when you know it. Use short, concise statements that owners, lenders, and insurers will understand. Build the documentation in a structured way, following the Uniformat and PPD organizations so information can be found quickly and in a consistent location.
Before design begins, the major elements for every project can be identified. Typically projects will require foundations, superstructure, exterior walls, and roof. The wall designed solution may not be known, but performance can be established to inform the design. Wind load, thermal, acoustic, and fire resistance are but a few performance characteristics that can be decided and documented without a designed solution. Moreover the resulting design can be measured against the documented criteria to ensure compliance and meeting the owner's requirements.
Identify each building element. Develop the content to a level of development consistent with the building model. Consider developing distinct elements within the building model matching the elements described in the Uniformat specifications and vice versa. Allow the specifications to describe the element components to minimize drawing notations. Coordinate the drawing keynote names with specification component names. Link the building model elements to the Uniformat specifications via the Uniformat element number, or title, or both. The relationship is one-to-one, and easily connected since both are organized by elements. Leverage the specifications references to minimize the need for internal building model data.
Develop the MasterFormat construction specifications to identify component technical requirements to allow the contractor to purchase and install the correct products as part of the Uniformat specified element. For instance, Uniformat specs will describe the interior partition as a whole with all its components including the studs, gypsum board, acoustic insulation, and acoustic sealant making up the partition. The MasterFormat spec will include the reference standards setting the gypsum board product quality, the submittal requirements to confirm the products meet the specifications, the installation requirements, and any technical requirements not included in the Uniformat specifications.
Maintain the Uniformat specification throughout the design process. Update and augment the data as more is learned about the design and the project requirements. Record the design process - include decisions affecting the design, and their rationale. Document design and performance criteria the owner will require to commission and ultimately operate the building successfully to achieve the predicted performance.
Make the entire process transparent and collaborative. Allow the owner, lender, contractor, subcontractor, material supplier, and any other stakeholder to actively participate, real time, in the specifications development within bounds set by permissions. Stakeholders given the opportunity will make the project better by protecting their own interests. Contractors want effective sequencing to simplify logistics. Subcontractors need easily buildable designs. Material suppliers want their products to be used correctly. Given the opportunity to participate, many if not all, requests for information and change orders may be eliminated saving the architect's valuable construction administration time.
Deliver both the Uniformat and MasterFormat specifications as record documents for the owner's use. Since MasterFormat specifications do not represent what was actually installed they will be of little value. Because Uniformat specifications contain design and performance criteria, they will be invaluable to the facility operations, maintenance, and future modification.
The owner will thank you.
[i] "Article 1 The Contract Documents," in Standard Form of Agreement between Owner and Contractor where the basis of payment is a stipulated sum. (American Institute of Architects: AIA Document A101, 2017) Article 1 enumerates each of the contract documents.
[ii] "SectionFormat Structure," in SectionFormat™ / PageFormat™ The Recommended Format for Construction Specifications Sections (The Construction Specifications Institute Construction Specifications Canada, 2008) This format prescribes the standard arrangement known as the 3-Part format using Part 1 - General, Part 2 - Products, and Part 3 - Execution. The format also includes standard article titles within each part for a consistent order of information within each specification.
[iii] MasterFormat® 2016 Update- Master List of Numbers and Titles for the Construction Industry (The Construction Specifications Institute Construction Specifications Canada, 2016). This standard includes nearly 9,000 numbers and titles used for construction specifications, detailed estimating, relating drawing notations to the specifications, and data filing. See MasterFormat. CSI membership or a recent purchase of MasterFormat is required for access.
[iv] Standard Classification for Building Elements and Related Sitework—UNIFORMAT II (ASTM International, ASTM E1557, 2009 Reapproved 2015). The original UNIFORMAT was developed jointly by the General Services Administration (GSA) and the American Institute of Architects (AIA) in 1972 for estimating and design cost analysis. UNIFORMAT II was first published in 1993 and enhanced the original, especially for the mechanical, electrical, plumbing, and fire protection elements. See http://www.uniformat.com for document background and application discussion.
[v] "Fundamentals and Formats Chapter FF/180 Preliminary Project Description (PPD)," in CSI Manual of Practice (The Construction Specifications Institute, 1996) PPDs are prepared to to describe the scope and relationships of major project elements and are organized in terms of building elements and components.
[vi] UniFormat™ A Uniform Classification of Construction Systems and Assemblies (The Construction Specifications Institute Construction Specifications Canada, 2010). This is a system for arrangement of construction information based on physical parts of a facility called functional elements, otherwise known as systems and assemblies.
[vii] PPDFormat™ A Guide for Developing Preliminary Project Descriptions (The Construction Specifications Institute, 2010). This is a guideline document for preparing and using Preliminary Project Descriptions (PPD). PPDFormat provides detailed information on preparing written documents to accompany Schematic Design phase drawings as contract deliverables and suggestions for other uses during early phases of the design of a facility. This author was responsible, in part, for developing PPDFormat.
[viii] ASTM E06.81 Building Economics Subcommittee previously chaired by Harold E. Marshall economist with National Institute of Science and Technology (NIST) and with the staunch UNIFORMAT II proponent and estimator Robert P. Charette, PE, CVS, PQS. This subcommittee developed standards to help evaluate building projects and reduce costs throughout the life cycle. This author acted as the CSI liaison to the ASTM committee relative to developments involving UNIFORMAT II and UniFormat.
[ix] Use of Uniformat estimates is evidenced by current project estimates for notable projects such as the Obama Presidential Library where three separate estimators furnished Uniformat estimates at the end of Schematic Design.
[x] "EA Prerequisite: Fundamental Commissioning and Verification," in LEED v4 for Building Design and Construction (U.S. Green Building Council, 2016) When LEED was first introduced required fundamental commissioning as a prerequisite. This commissioning initially required a Basis of Design document to establish the criteria by which the building energy systems were commissioned. Today LEED requires Owner Project Requirements in addition to the Basis of Design as documentation to support commissioning.
[xi] Harold E. Marshall, Harold E, and Charette, Robert P. UNIFORMAT II Elemental Classification for Building Specifications, Cost Estimating, and Cost Analysis (National Institute of Science and Technology, NISTIR 6389, 1999). This paper was written to ensure consistency in the economic evaluation of building projects over time and from project to project, and it enhances project management and reporting at all stages of the building life cycle. See http://portal.ct.gov/-/media/DAS/Office-of-School-Construction-Grants/Task-188---Required-Forms-Regarding-Plan-Review-and-Approval/FORM-SCG-2020-UNIFORMAT-II-classification-for-building-cost-estimating-4-24-17-KD.pdf